Chassis Dyno Basics – Here’s What it Does
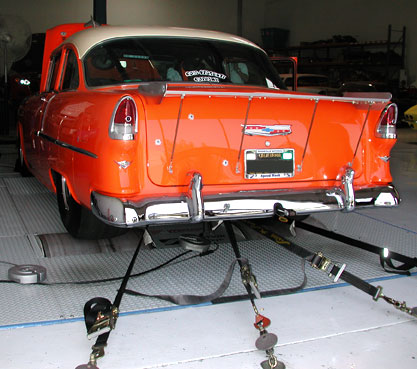
A chassis dyno is used to measure the amount of horsepower and torque a vehicle produces at the wheel’s axles. The dyno replicates what a street or track vehicle would experience for these values. It is possible to do before/after testing in a controlled environment where the same test can be run back-to-back on the dyno to gather baseline horsepower and torque statistics (i.e., a starting point).
Using an optical wheel tachometer, the rpm signal from the engine is picked up. Engine speed data can be collected with this device’s magnetic base and an infrared beam and reflective tape, often on the engine’s harmonic balancer.
Load vs. Inertia
Diesel engineers know that putting the engine under strain increases turbo boost pressure, which is essential for simulating the kind of boost a truck would experience on a street or track. Most diesel enthusiasts prefer to run their vehicles on a load cell dyno rather than an inertia-only dyno because boost is such an essential component of the power-making equation on a diesel. Electromagnetic power absorbers are commonly used in load cell dynos for applying load to test vehicles. If you’re looking for an adjustable electronic braking system, you’ve found it with this device. As a rule, heavier loads are required to produce the most accurate horsepower estimates in higher horsepower vehicles (with larger, more difficult-to-spool turbochargers).
Inertia dynos have no electrical or water-based stress on the car, and other than the weight of the rollers, there is no other load on the vehicle. The rollers’ acceleration rate on an inertia dyno is used to calculate horsepower. Pure-inertia dynos are more difficult for diesel trucks to be loaded to maximum boost. However, despite the lower numbers, experienced dyno operators can still obtain good results with the correct technique and know-how.
Power-braking the car is the most typical approach to generate enough boost on an inertia dyno. When the brakes are applied, and the rollers are accelerated simultaneously, the engine is loaded, allowing the boost to rise gradually, even before the dyno test begins.
SuperFlow Chassis Dyno
An extensive range of state-of-the-art load cell chassis dynos, engine dynos, transmission dynos, and flow benches from SuperFlow is well-known in the automotive industry. It’s most common to see the AutoDyn 849 model with a two-wheel drive.
It has two 42-inch rollers with knurled surfaces for maximum traction, two eddy current absorbers (brakes), and 1,600hp of loaded absorption capabilities.
Correction Factors
Bringing up the subject of correction factors can be an absolute minefield. They’re adored by some and loathed by others. Uncorrected dyno statistics hold more weight in the eyes of this enthusiast than corrected ones. Because correction factors are used to show how much horsepower and torque a vehicle would have produced in ideal conditions, therefore. Because of this, it’s not always possible to get the best possible outcome. Besides, how many of us have dynoed at sea level, on a 60-degree day, with unusually low relative humidity and 29.92 inHg appearing on the barometer?
Uncorrected data from a dyno test tells us that our truck produced the horsepower and torque ratings on this day and under these weather conditions. Three different correction factors are visible on the dyno graph displayed below, but which one is the most accurate?
Don’t Forget Engine Dynos!
Engine dynamometer testing is alive and well, even though chassis dynos get all the attention in the diesel world. The crankshaft or flywheel is directly connected to the dyno in the upper echelon of truck pulling. The trucks have one-speed transmissions, and a chassis dyno is impractical or impossible to test them on. There will be no damage to the transmission in this situation.