Cold Hard Facts to Know About Chassis Dyno Testing
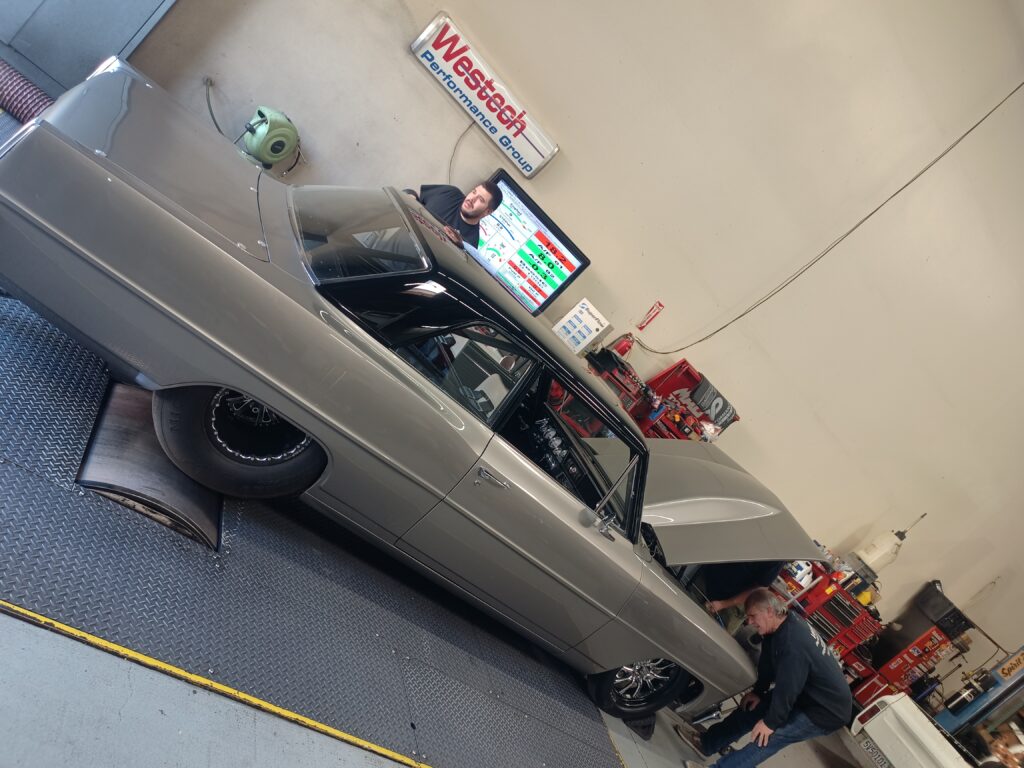
In the past twenty years, chassis dynos operating in shops have increased across the country dramatically, making it theoretically possible for the masses to evaluate their engine’s performance as it is installed in the vehicle and compare the results with their friends’ cars. In practice, this has made it possible for enthusiasts to compete with one another. However, this is predicated on the assumptions that the results obtained at one site may be directly compared to those acquired at other facilities and that the results accurately reflect the actual power output of the tested vehicle. There is also the issue of the degree of accuracy, which refers to whether the typical dyno shop can adequately analyze the actual effect of modest, incremental alterations, particularly on late-model automobiles and trucks. Read on to find out the unvarnished truth about chassis dyno testing, then proceed to this article’s next section.
What are the primary categories of chassis dynos that are available for purchase today?
The chassis dynos used in modern vehicles fall into one of these three basic categories: electric dynos, water-brake or hydraulic dynos, or inertia dynos. Both the outcomes of tests and the kinds of tests that can be performed are impacted by the dynamometer being used. The best modern load-bearing hydraulic and electric dynos with sophisticated control software can do step tests, constant-speed pulls, and even part-throttle testing to the point where full vehicle road-load simulations can be conducted right on the dyno. On the other hand, a pure inertia dyno can only do full-throttle acceleration runs.
How exactly does an inertia dyno measure force?
The horsepower output can be extrapolated with inertia dynos by evaluating the acceleration rate of the dyno drum with the help of a sophisticated accelerometer and computer software. An inertia dyno is only applicable when the tested vehicle is in motion and gaining speed. It uses large roller drums with known masses mounted on bearings that enable free rotation of the drums. After positioning a car such that its drive wheels are resting on the rollers of the dyno, the vehicle is ready to be tested.
After engaging the appropriate gear, rapid acceleration is initiated with the wide throttle. The tires need a specific time and are forced to move the heavy rollers faster. According to the fundamental postulates of physics, the rate of acceleration is directly proportional to the amount of energy exerted by the tires on the heavy roller to cause it to rotate. The dyno software keeps track of the velocity of the rollers as well as the amount of time it takes to reach a specific rate of acceleration.
Then it determines the amount of power available to the rear wheels. The software then graphs the power and gear-compensated engine torque versus the engine’s revolutions per minute using the data from an inductive probe mounted on the machine. Some inertia dynos also attempt to estimate the power and torque produced by the flywheel based on mathematical models and information from additional sensors.
Since a dyno that solely measures inertia can only compute power by determining the rate of change in acceleration (which is why it is called an inertia dyno), this dyno cannot do loaded testing or step tests. Because load tests cannot be performed, it is impossible to precisely develop optimal timing and fuel curves that can be utilized in various driving scenarios.
If the inertial test function can be combined with a strain gauge to change the rollers’ inertia trim effectively—as is possible on higher-end multifunction dynos—extraordinarily light or heavy vehicles might fall off the curve, and turbocharged engines won’t build boost as they do in the real world. On the other hand, while working with standard automobiles weighing roughly 3,500 pounds, it is possible to achieve reproducible outcomes in a short amount of time with very little preparation required.
The Dynojet is currently the most popular brand of pure-inertia dynamometers, but some of the company’s most recent models also come with an eddy-current option (see below).
How does a hydraulic dyno work?
The hydraulic or water-brake dyno, which operates in a manner analogous to that of standard engine dynamos, is dependent on a constant speed brake or absorber attached to a rotor that consists of both a spinning element and a stationary element. On a chassis dyno, the tires move rollers that are then coupled to the rotor, but on an engine dyno, the flywheel is immediately connected to the rotor of the dyno.
In theory, current dynamometer software can compensate for all of this, even though the vast rotor mass both stores energy and provides an inertial mass that needs to be overcome. The only Dynapack hydraulic dyno is an exception since its load brake is attached directly to the axle. This eliminates the need for tires and rollers in the testing process.
In either case, the rotor parts’ ability to generate braking force is utilized to absorb or equal the motor’s output. Depending on the application, water or hydraulic fluid can be used to produce the braking force. It is possible to calculate the horsepower production of the rotor by using a strain gauge to measure the torque reaction between the rotor’s spinning and stationary elements. This works in the same manner as an engine dyno.
However, some hydraulic dyno manufacturers, such as Dynapack, do not use a strain gauge and instead measure the fluid (hydraulic) power required to hold a vehicle at a constant rpm (the formula for calculating horsepower is as follows: horsepower = [gallons per minute of flow through the rotor x psi] 1,713). In principle, the horsepower of the fluid should be equivalent to the vehicle’s power.
The disadvantages of a hydraulic dyno are the same as those of engine dynos with comparable configurations. When you first snap the throttle wide open, there will be a tiny lag while the impeller chamber fills up with fluid. This will translate into a slight lag in the acceleration of the vehicle.
Because of this, the mechanism will initially lack accuracy until it has a chance to stabilize. There is a workaround provided by Dynapack in the form of an optional “start-point stabilize” option. This option maintains a constant rpm at the beginning of the test until the engine stabilizes. Hydraulic dynos must be calibrated regularly since their accuracy can gradually deteriorate over time if the equipment is not maintained correctly.
What is the function of an electric dyno?
How do the readings from the chassis dyno compare to those from the engine dyno? Is there any accuracy with which one can forecast the quantity of power lost throughout the drivetrain?
Temperature, airflow, barometric pressure, and torque calibration are only a few of the characteristics shared by all dynos, including engine dynos, that play a role in determining how accurate the test results are. On the other hand, the findings of a chassis dyno can be affected by a significant number of extra parameters. These elements are far more challenging to regulate than the factors generally encountered on an engine dyno.
Variables that affect drivetrain losses include gear selection (testing should typically be done in the transmission’s 1:1 gear to minimize the impact of this factor), fluid temperatures, acceleration/load factors, drivetrain inertia, brake drag, the method of securing the vehicle to the ground, the weight that is distributed over the axle, and tire selection, growth, and slippage.
While using an engine dyno, it is analogous to weighing oneself naked; when using a chassis dyno, it is like attempting to weigh oneself while wearing clothes, in which case you might have shoes, you might have pants, you might have wet clothes, or you might have dry clothes.
Even though some of the most recent dyno software includes complex formulas and assumptions to correlate rear-wheel numbers with flywheel numbers, there is no way to measure, predict, or otherwise determine engine flywheel power from a chassis-dyno test with any repeatable certainty, mainly when using a standard acceleration test. This is because a chassis dyno test only measures the energy transmitted to the vehicle’s rear wheels.
People typically assert that the loss in powertrain efficiency is approximately 10 percent when using a manual transmission and between 15 and 18 percent when using an automatic transmission. But what does that percentage represent about the total? 15 percent of 400 horsepower is not the same as 15 percent of 700. The difference between rear-wheel horsepower + 15 percent and flywheel horsepower minus 15 percent is significant. The drivetrains of late-model cars are typically more efficient (they experience fewer losses) than the drivetrains in old muscle cars. Therefore, determining a specific number is, at best, an estimate, and, in a way, it is irrelevant:
The objective should be to end up traveling faster. This requires knowing where you are, what works and what doesn’t, and how to get to where you want to be to get the desired result of having more helpful force at the wheels in every gear. It will be faster if it has better tires, more air, more gasoline, more efficient drivetrain elements, and better gear selection and tune. The comparison of the power of the engine to the power of the wheels is a distraction.
Performing a loaded step test on each system while stabilizing the engine at each selected test rpm point is the most accurate and repeatable approach to compare the findings obtained from an engine dyno and a chassis dyno. If you absolutely must make a comparison, this is the chosen method. In an ideal scenario, you would do both tests in an environment with the same temperature and humidity, ensuring that the coolant and oil temperatures are comparable. Any discrepancy still would provide a reasonably accurate assessment of the parasitic losses that occur throughout the drivetrain.