The Basics About Different Types of Chassis Dyno Testing
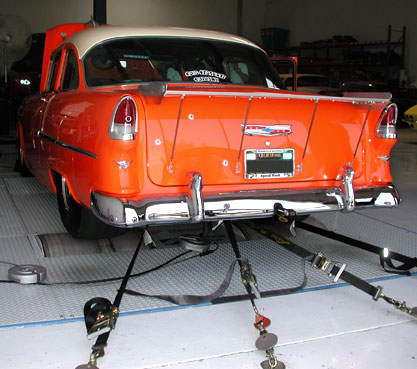
Over the last twenty years, chassis dynos have spread across the country, making it possible for the average person to see how their car’s engine performs and compare it to the results of their friends’ cars. But this assumes that results from one facility can be compared to results from other facilities and that the results accurately show the true power output of the test vehicle. There’s also the question of accuracy, or whether the average dyno shop can accurately measure the true effect of small, incremental changes, especially on computer-controlled cars with a lot of power.
Inertia dynos, water-brake or hydraulic dynos, and electric dynos are the three main chassis dynos still used today. The type of dyno affects how well tests work and what tests can be done. It can only do full-throttle acceleration runs on a pure inertia dyno. The best modern load-bearing hydraulic and electric dynos with sophisticated control software can do step tests, constant-speed pulls, and even part-throttle tests to the point where full vehicle road-load simulations can be done right on the dyno itself.
How does an inertia dyno work?
Inertia dynos figure out how much horsepower a car has by looking at how quickly the dyno drum moves. They use a sophisticated accelerometer and computer software to do this. It only works when the car is going faster. It has heavy roller drums with a known mass mounted on bearings that let them freely move around. The drive wheels of a car are placed on the rollers on the dyno. Here’s how it works: It takes a lot of time and force for the tires to move the heavy rollers. A car’s acceleration rate is related to how much power its tires put on the heavy roller to get it to move.
The software that runs on the dyno keeps an eye on the speed of the rollers and how long it takes to get to a certain speed. It then estimates how much power the rear wheels have. When the software gets data from an inductive probe on the engine, it then graphs the power and gear-compensated engine torque against engine rpm, as shown in the figure. Some inertia dynos also try to figure out how much power and torque a flywheel has used mathematical models and extra sensors.
To figure out power, pure inertia-only dynos only look at acceleration changes. This is why it’s called an inertia dyno. It can’t do loaded tests or step tests because of this. You can’t do load tests, which makes it hard to figure out the best timing and fuel curves for different driving situations.
Today’s inertial dynos don’t let you change the weight or resistance of the static rollers to match the vehicle’s weight. If the dyno software and strain gauge can effectively change the rollers’ inertia trim—which is possible on higher-end multifunction dynos—extremely light or heavy vehicles might fall off the curve, and turbocharged engines might fall off the curve won’t build boost as they do in the real world.
On the other hand, with cars that weigh about 3,500 pounds, the results can be repeated with very little set-up time. It is the most common pure-inertia dyno today, but some of Dynojet’s newer models can also be used with eddy currents (see below).
How does a hydraulic dyno work?
The hydraulic or water-brake dyno works like a typical engine dyno. It has a constant speed brake or absorber connected to a rotor with a rotating element and a stationary element. On an engine dyno, the flywheel is connected to the dyno’s rotor, but on a chassis dyno, the tires turn rollers that then connect to the rotor of the dyno.
Modern dyno software should be able to account for all of this, even though the large rotor mass stores energy and has to be overcome. The Dynapack hydraulic dyno is an exception because the load brake is attached directly to the axle. This means that tires or rollers are not in the picture.
Any time the brakes are used, they produce a force used to absorb or match the powertrain output. Water or hydraulic fluid gives the brakes their power. A strain gauge can be used to measure the torque reaction between the rotor’s rotating element and a stationary element and then (just like an engine dyno) figure out how much horsepower the rotor can put out. Manufacturers like Dynapack don’t use strain gauges when making hydraulic dyno machines. Instead, they use a formula to figure out how much fluid (hydraulic) power is needed to keep a car at the same speed. The fluid horsepower should be the same as the power of the car.
Hydraulic dynos have the same problem as engine dynos that are the same way. There is a little lag while the impeller cavity is filled with fluid, which means there is a little lag when you first open the throttle wide. This causes the mechanism to be a little off until it gets used to it.
Dynapack has a “start-point stabilize” option that keeps the rpm steady at the start of the test until the engine has cooled down. Hydraulic dynos need to be calibrated regularly because the device’s accuracy can go down over time if it isn’t properly cared for.
How does an electric dyno work?
How do chassis-dyno readings compare to readings from the engine-dyno machine? In some ways, yes. Is it possible to predict how much power is lost through the drivetrain?
Temperature, airflow, barometric pressure, and torque calibration are all things that can affect how accurate a test is. All dynos, including engine dynos, have these things in common. But on chassis dynos, there are many more things that can affect the results, which are more difficult to control than on an engine dyno.
Losses in the drivetrain can change based on the gears used, the temperature of the fluids, the speed at which the vehicle is moving, and other factors. Testing should usually be done in the transmission’s 1:1 gear to minimize this factor.
It’s the best way to compare the results of an engine dyno with those of a chassis dyno. Run a loaded step test on each system, stabilizing the engine at each chosen test rpm point. Ideally, it would help if you did both tests in the same environment, ensuring that the coolant and oil temperature are the same. Any remaining difference would give a pretty good idea of the parasitic losses through the drivetrain.